Advanced Demo
for “Importing and Flattening a Carbon Fibre Air Intake”
This video will present the import and the flattening process for a composite part, a carbon fibre air intake. Going from a 3D model to 2D digital patterning, ExactFlat can help do more work in less time. In this demo we use a carbon fibre air intake and import it into ExactFlat for Rhino 3D. We work on the imported model, flatten it into 2D patterns and create and export file for the cutter.
Table of Contents
Here’s the table of contents to the “Importing and Flattening a Carbon Fibre Air Intake” video. This video shows how to flatten from 3D to 2D and create better patterns faster. Use the links below to navigate to the section of interest or watch the entire video:
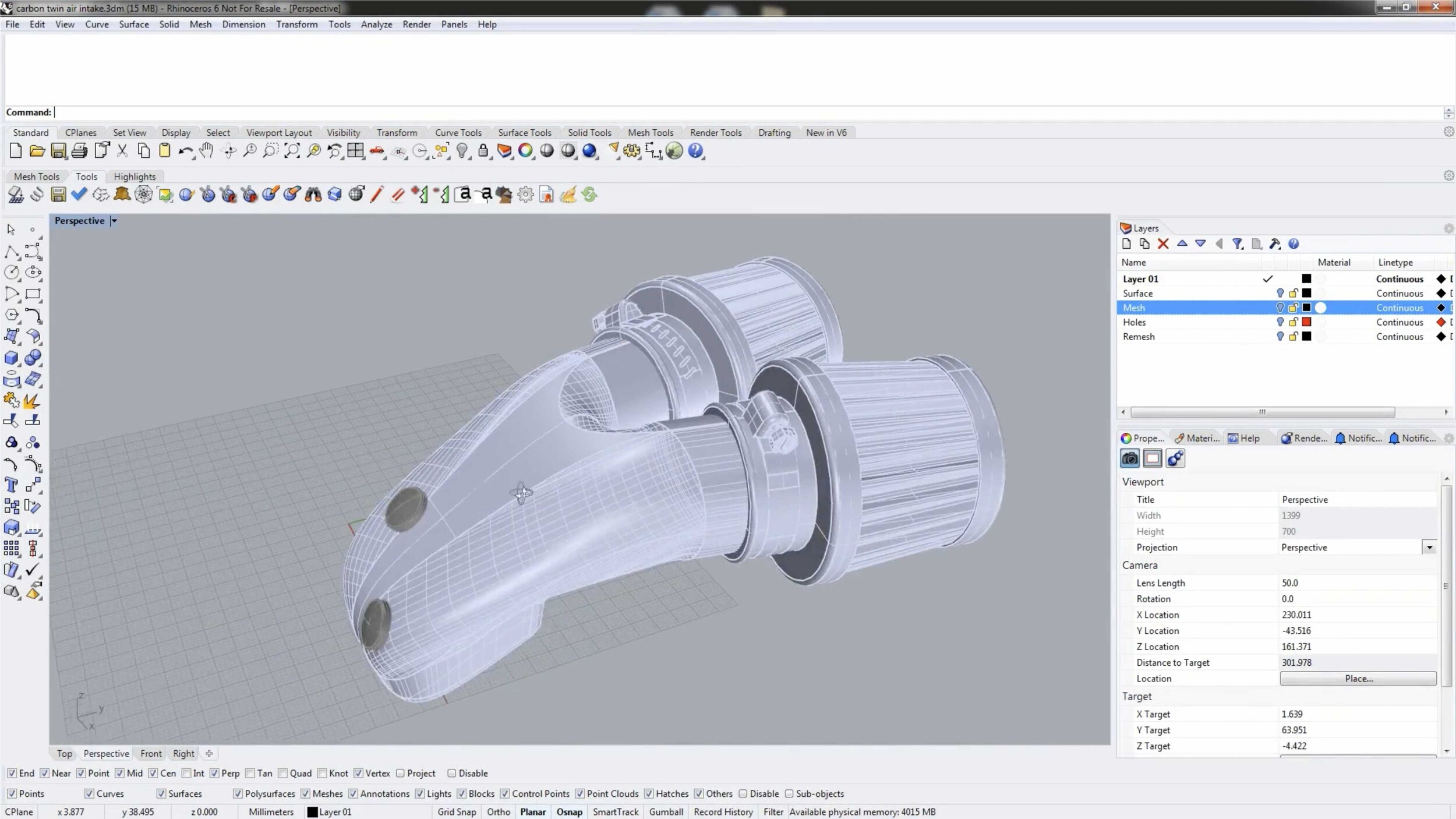
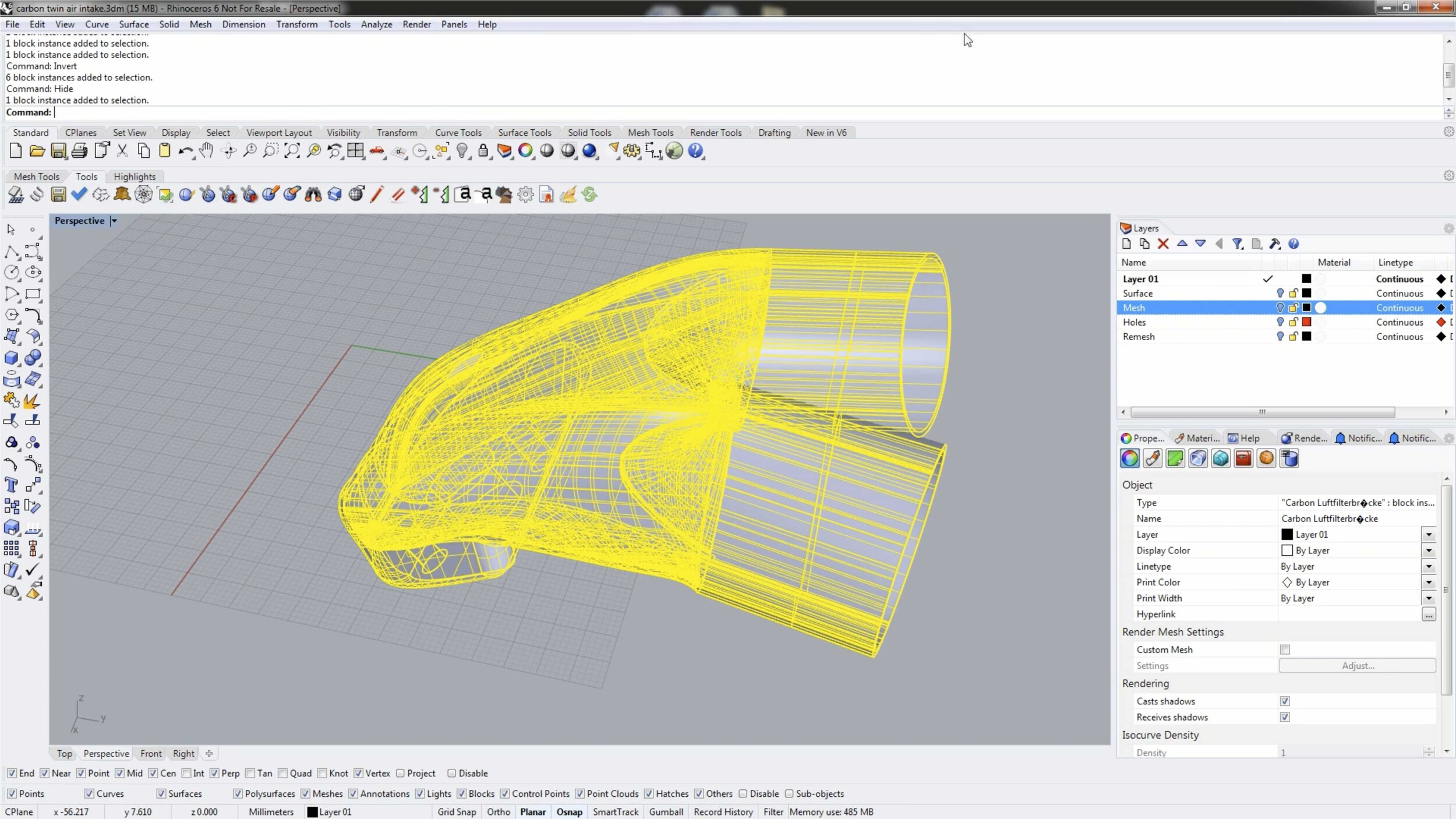
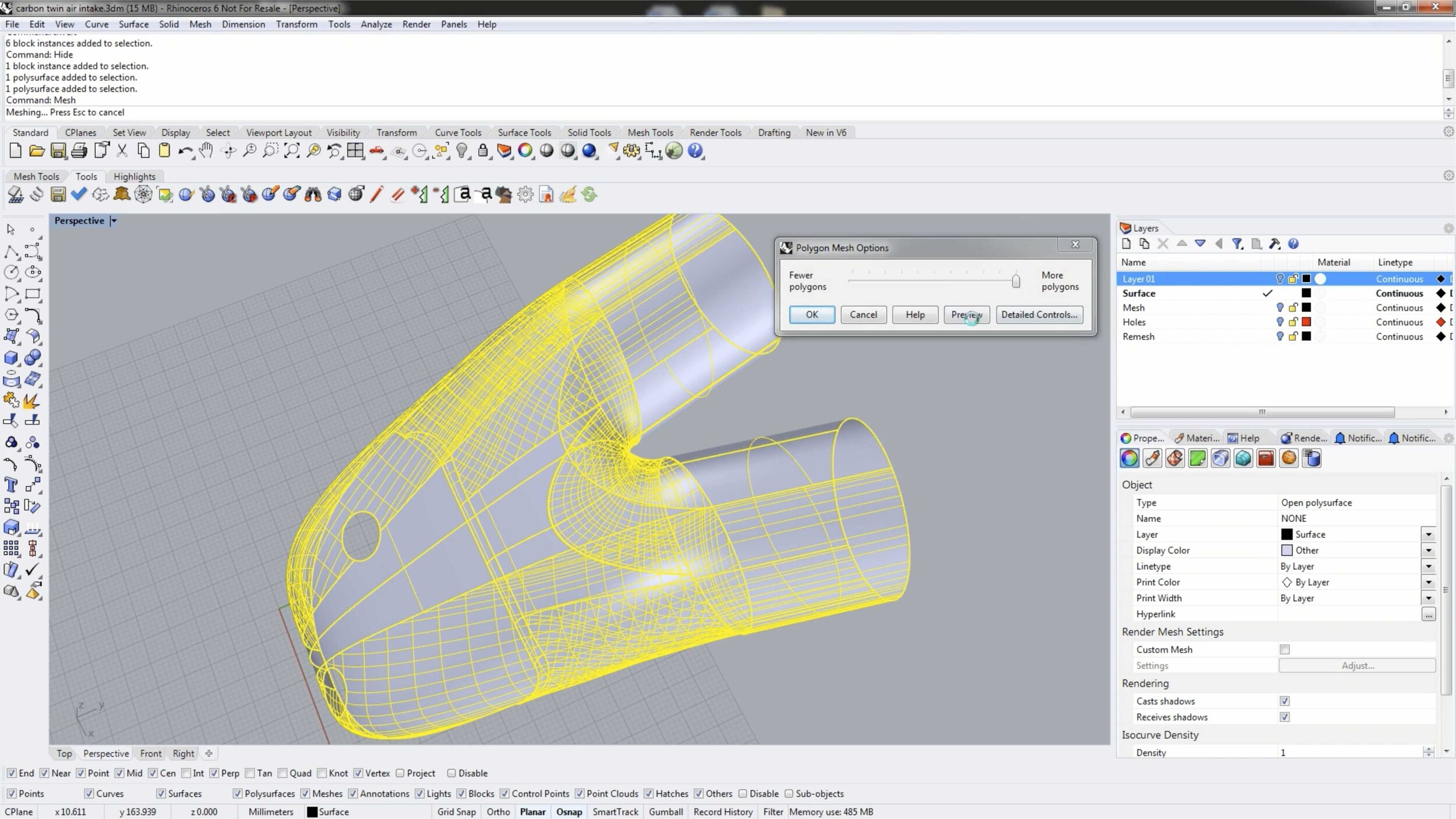
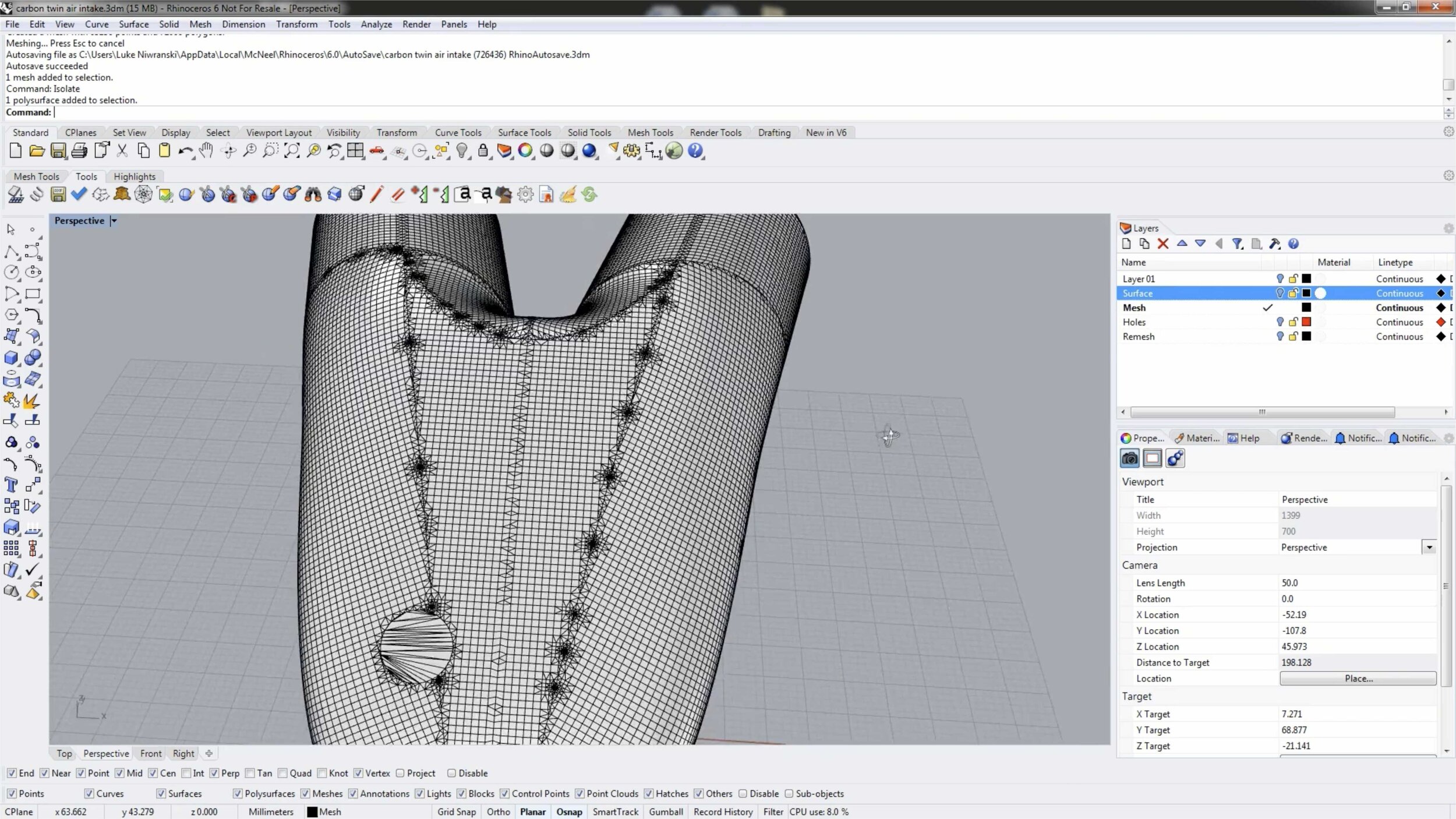
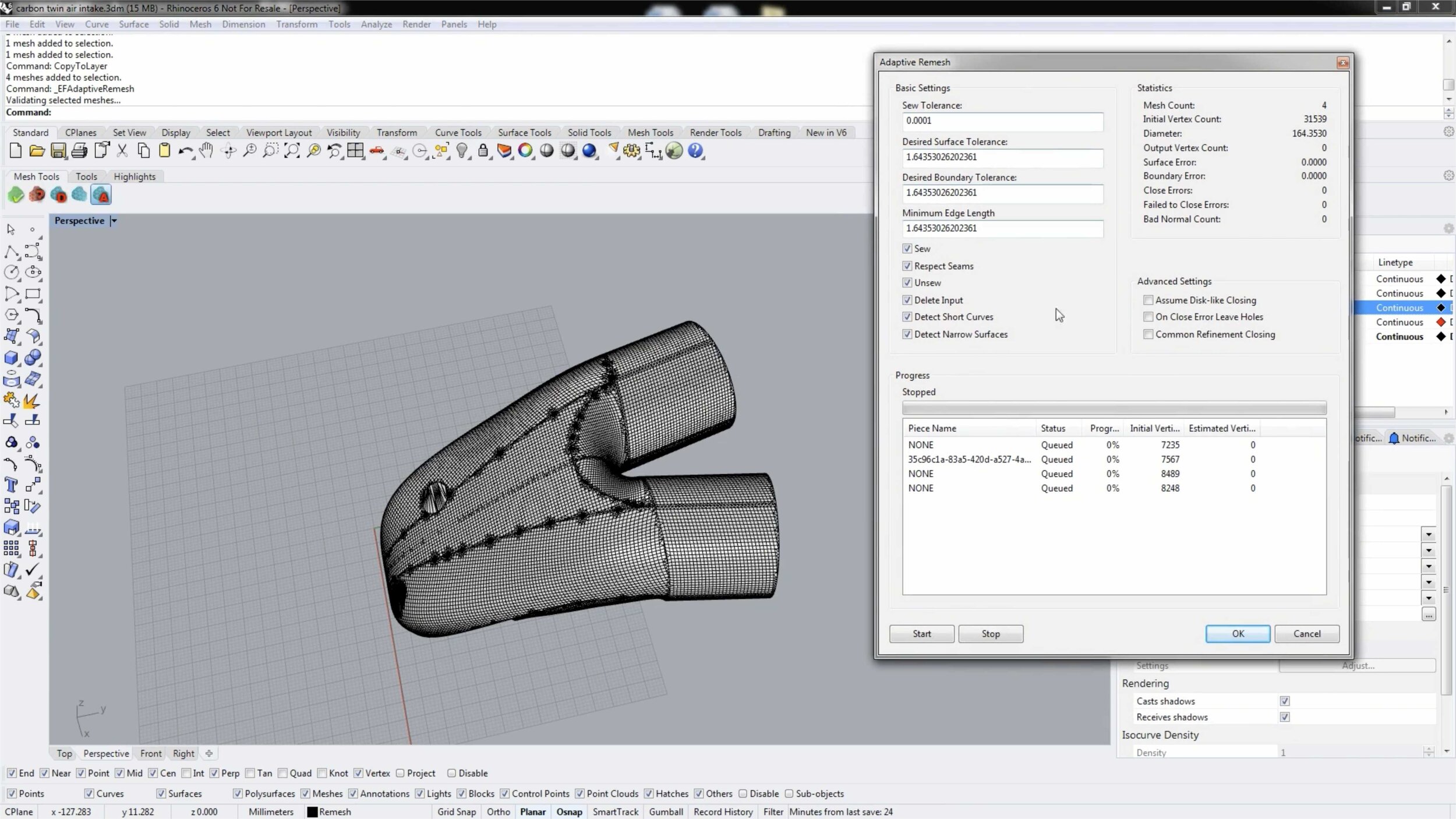
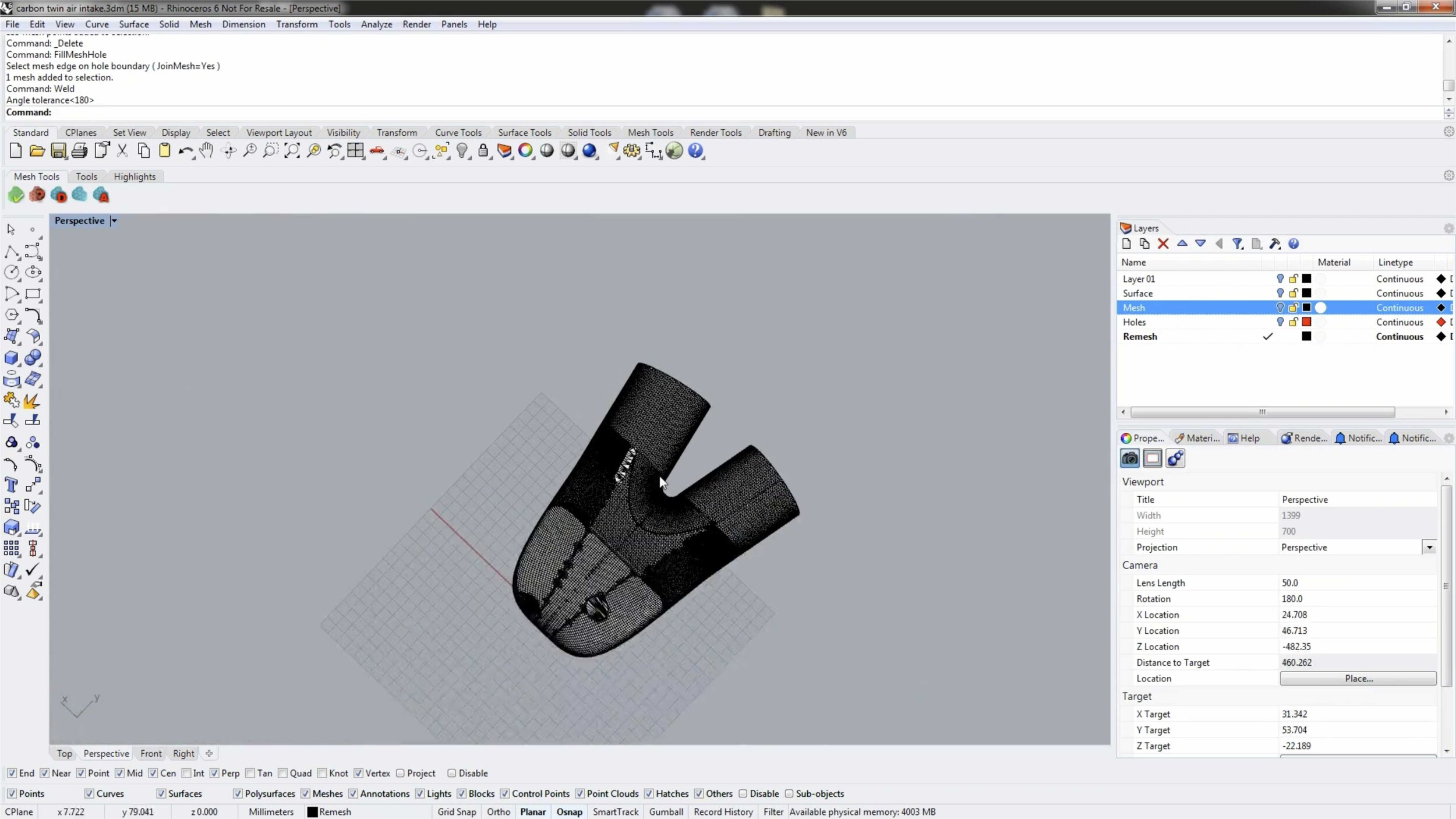
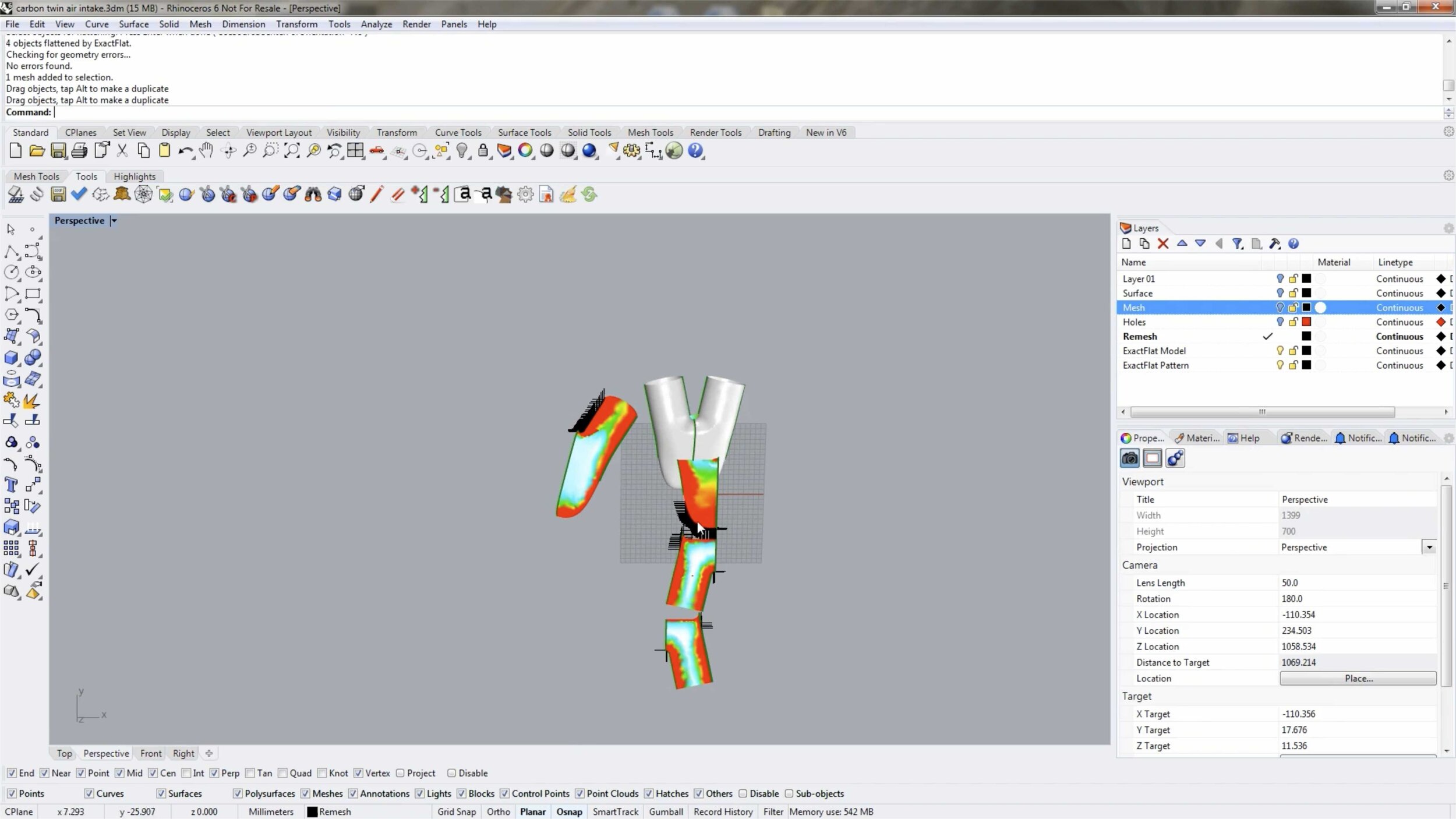
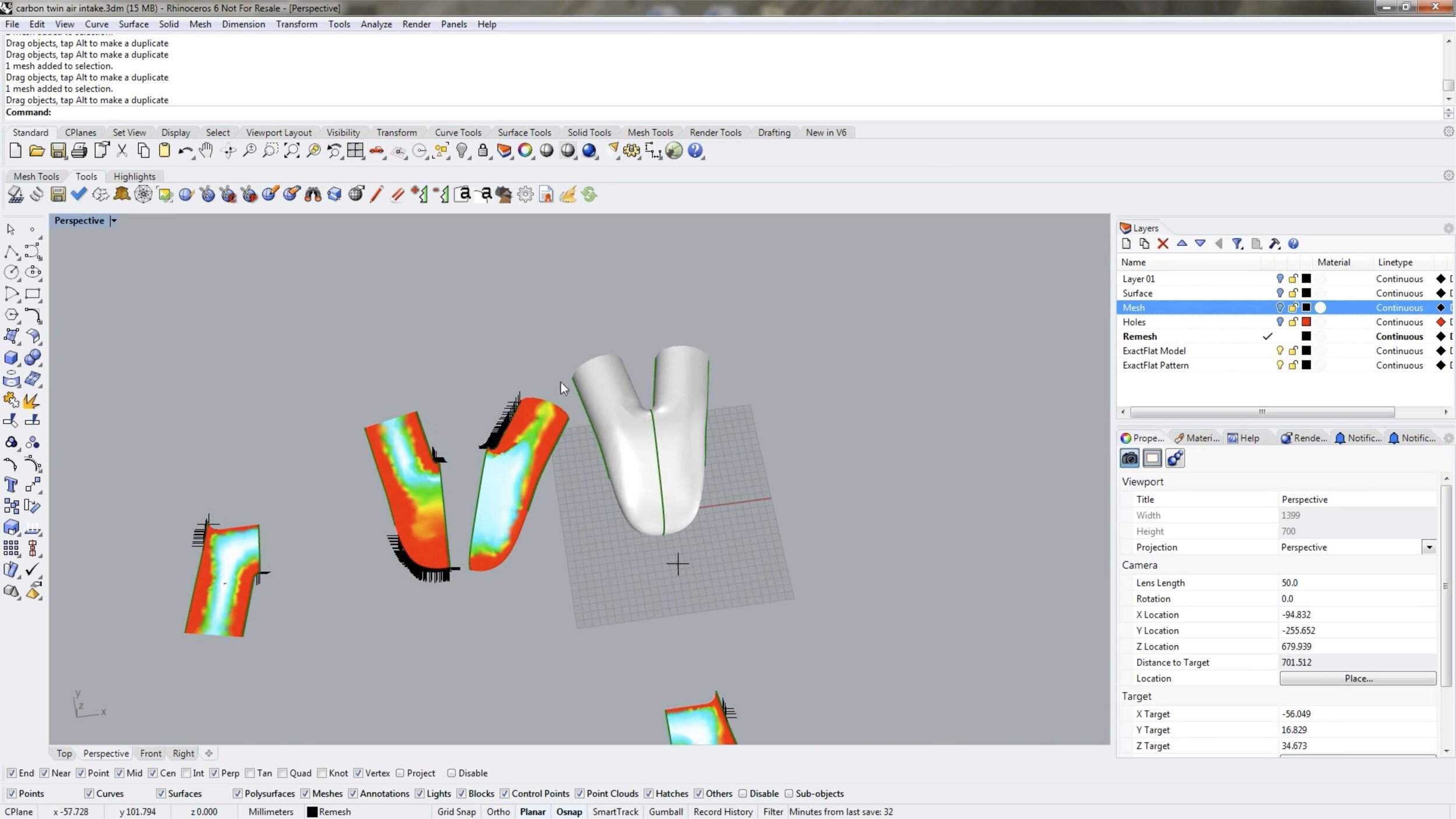
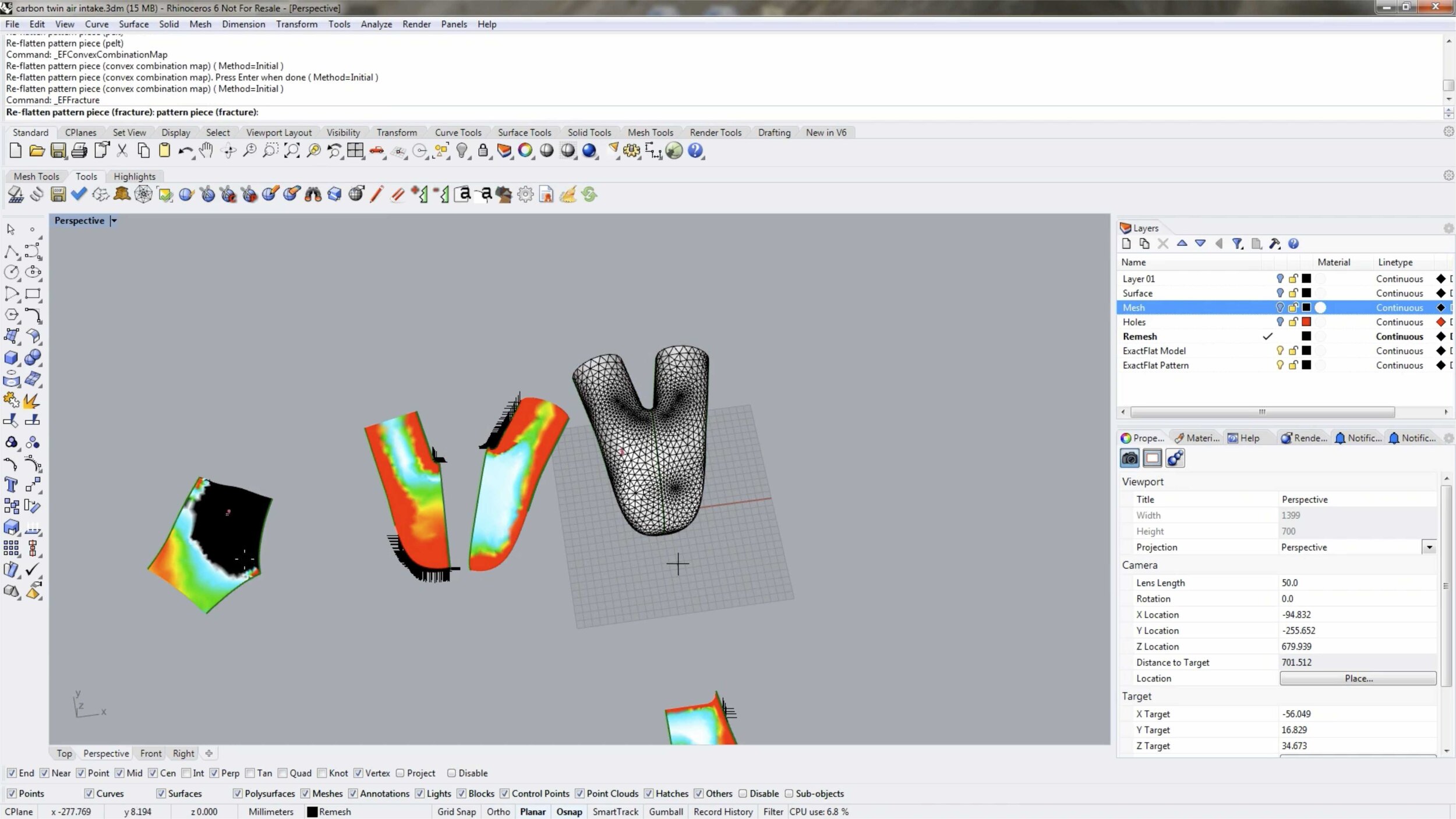
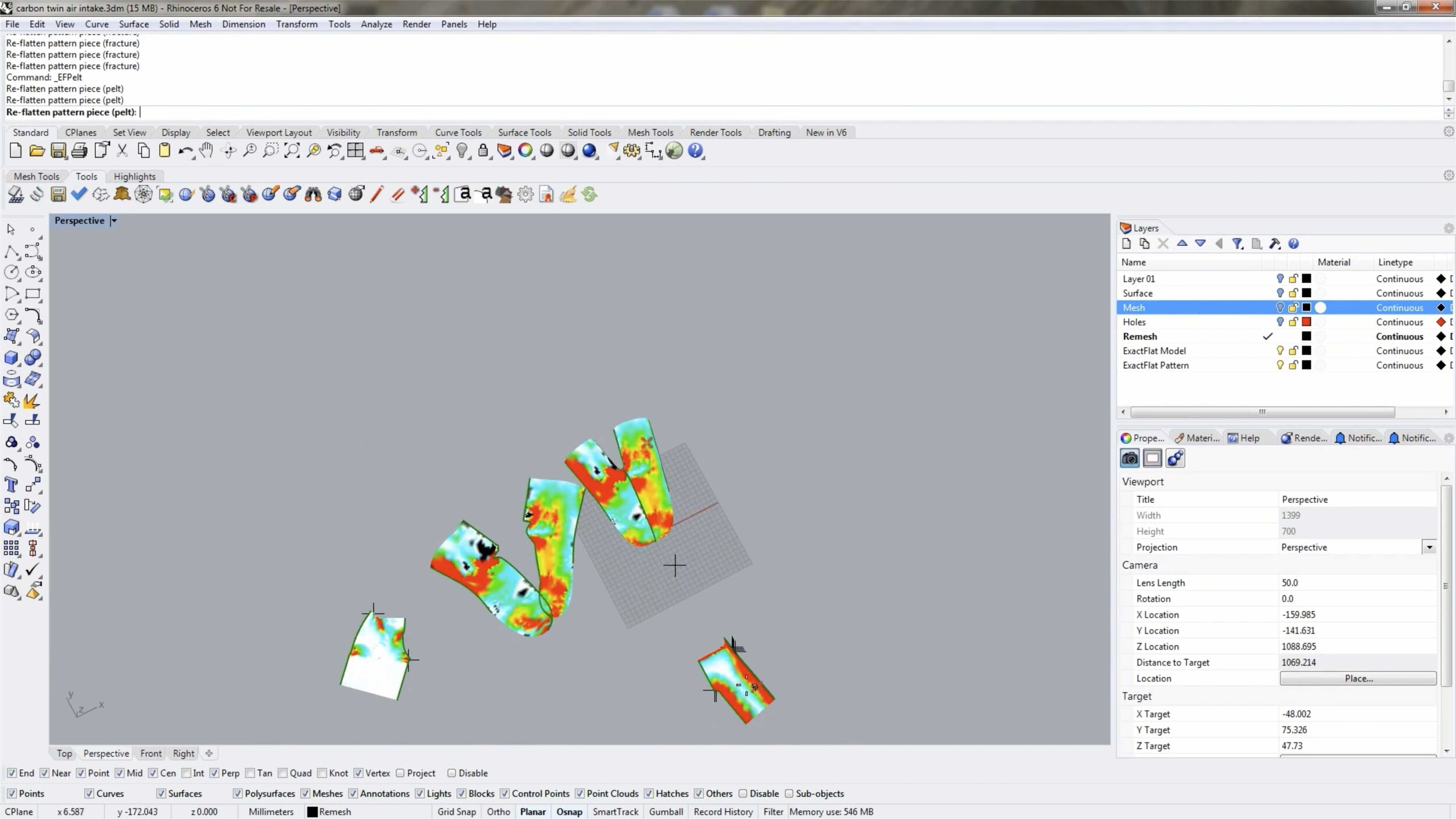
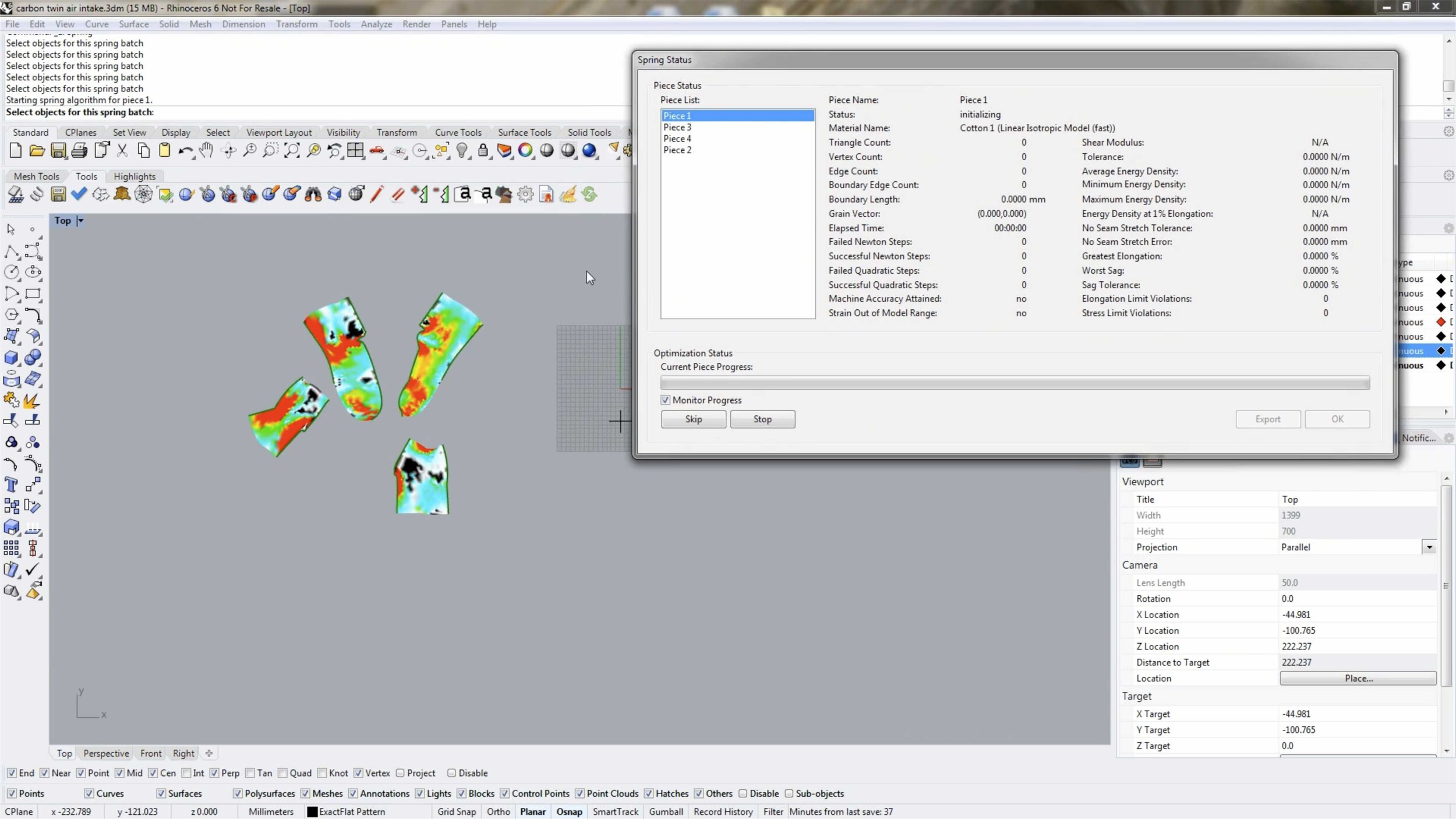
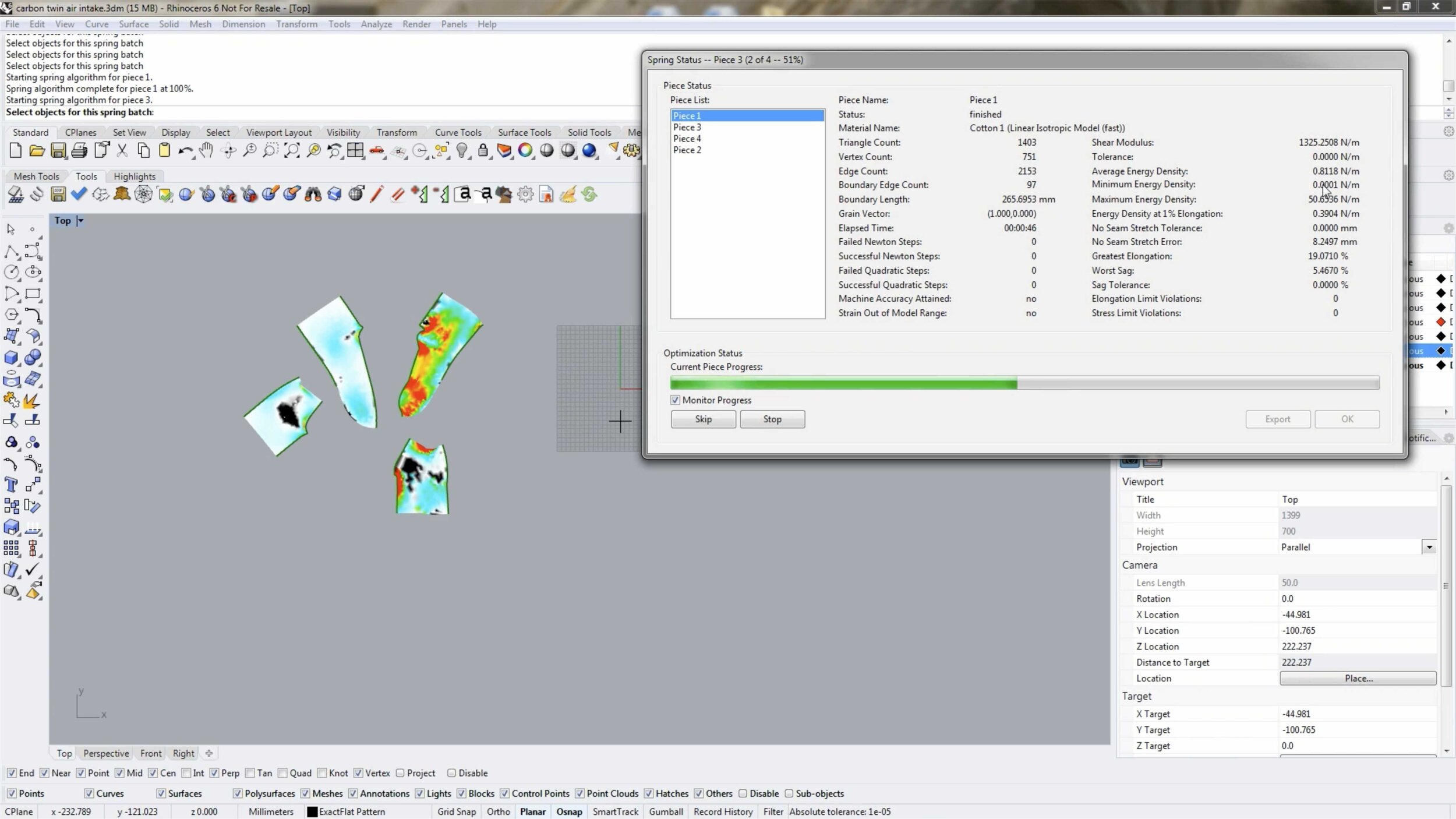
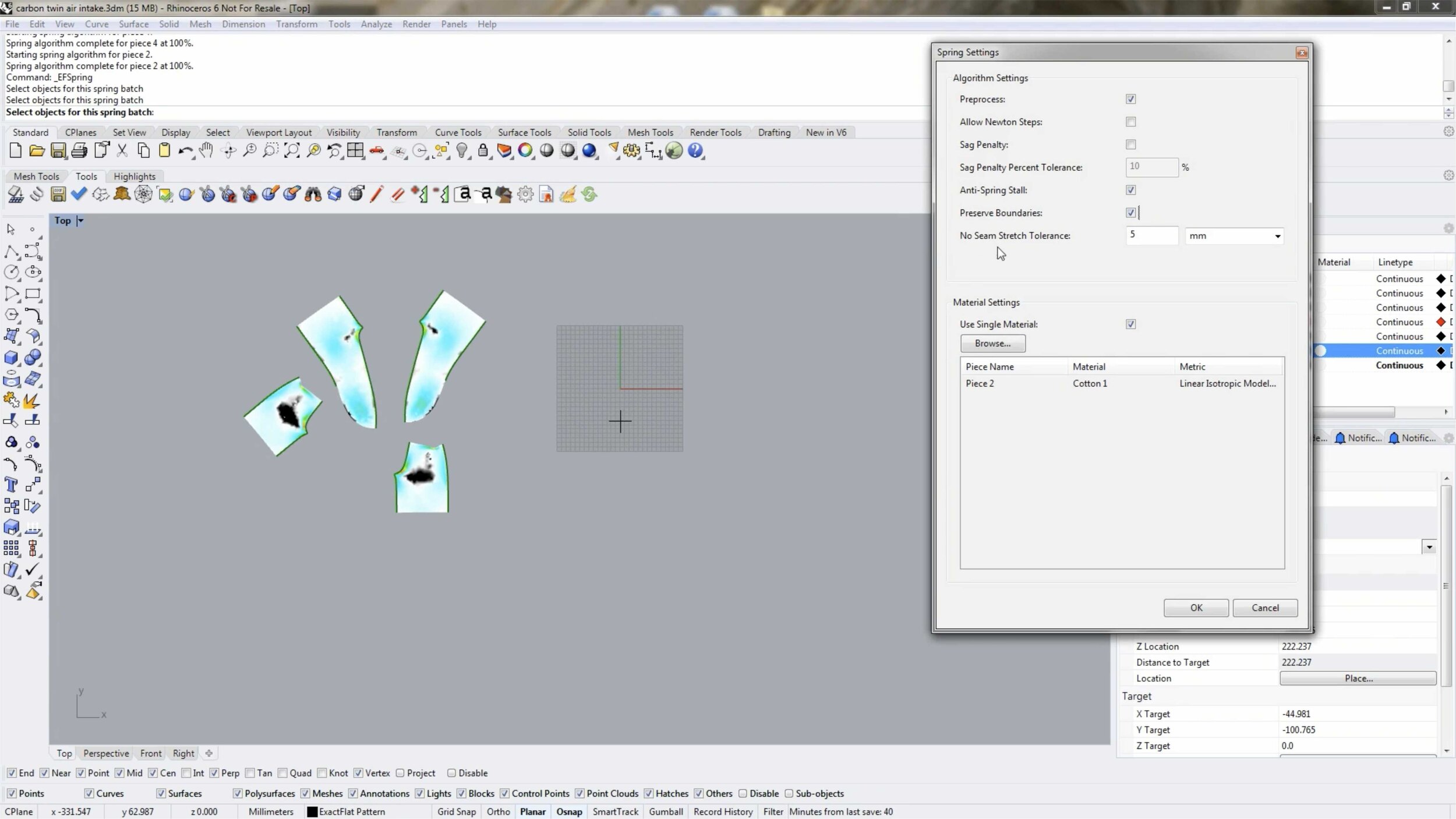
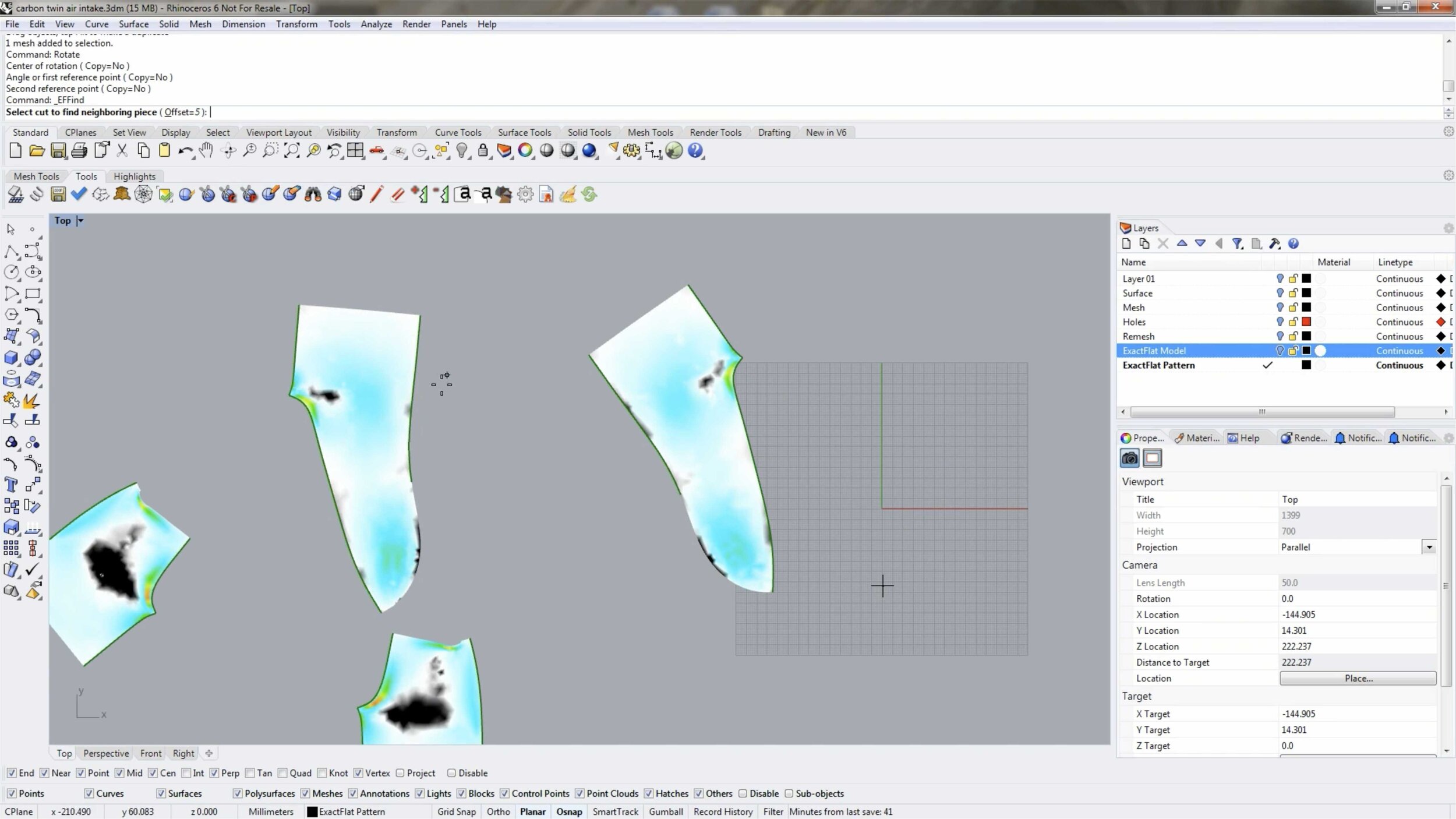
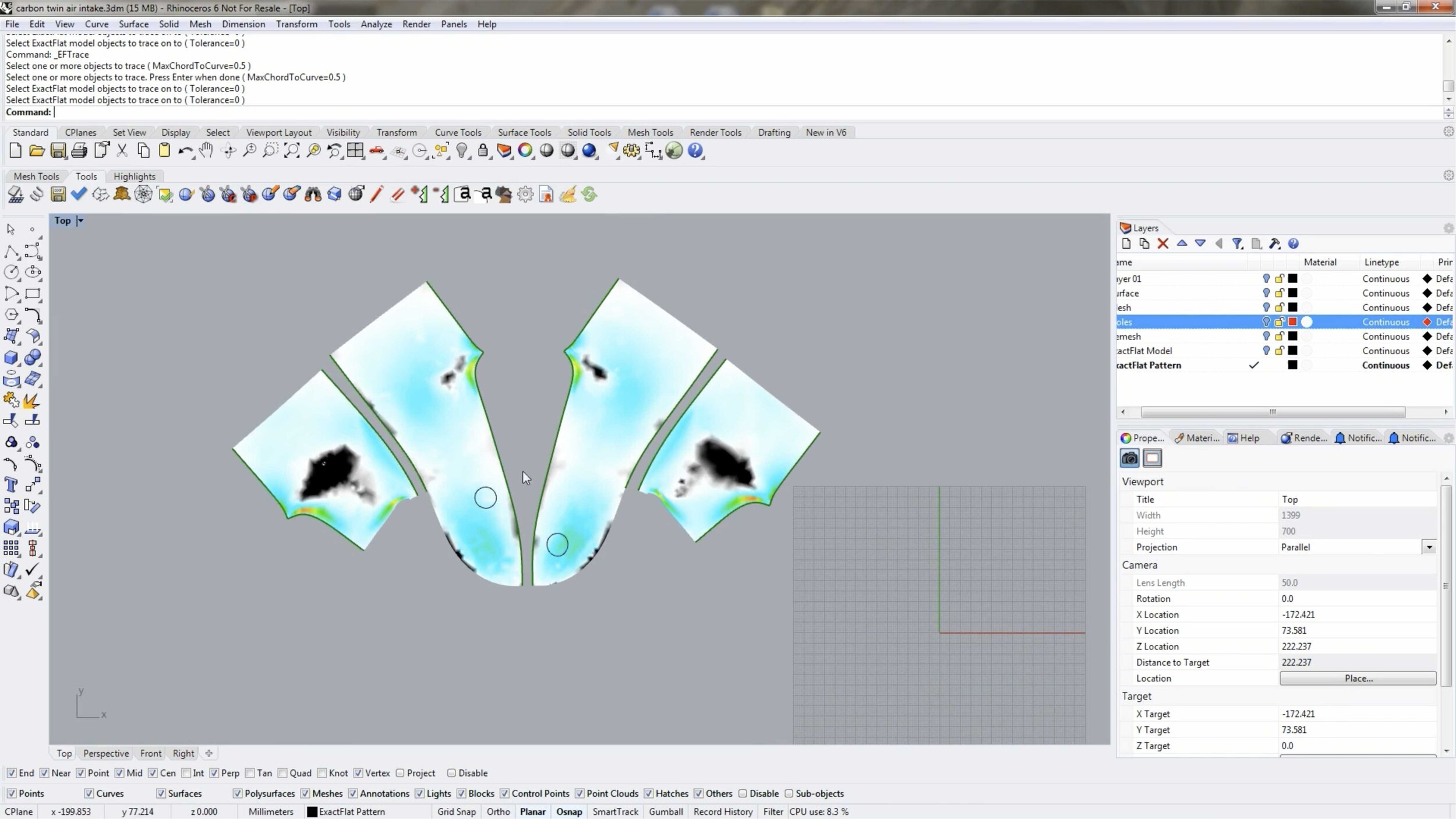
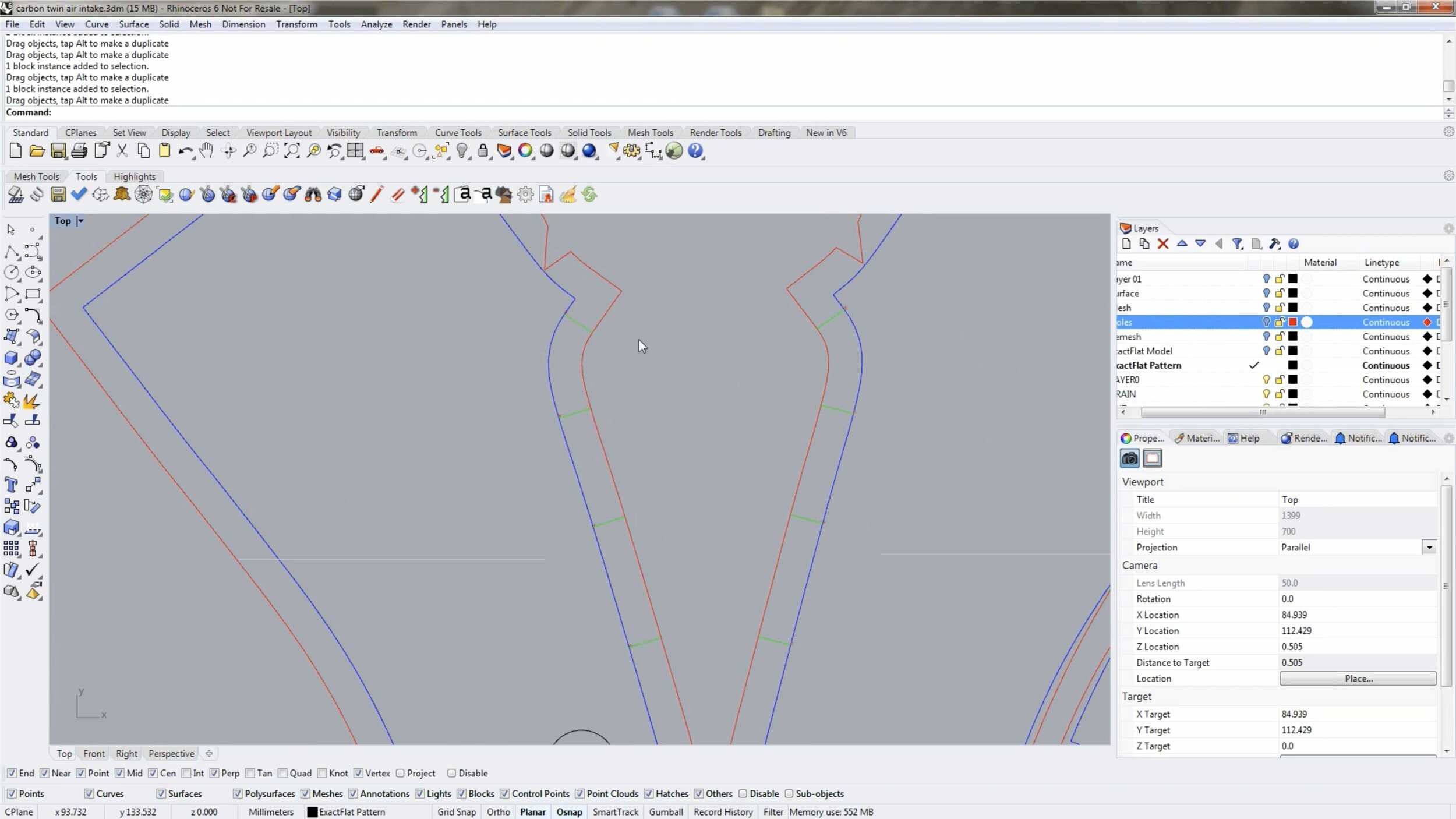
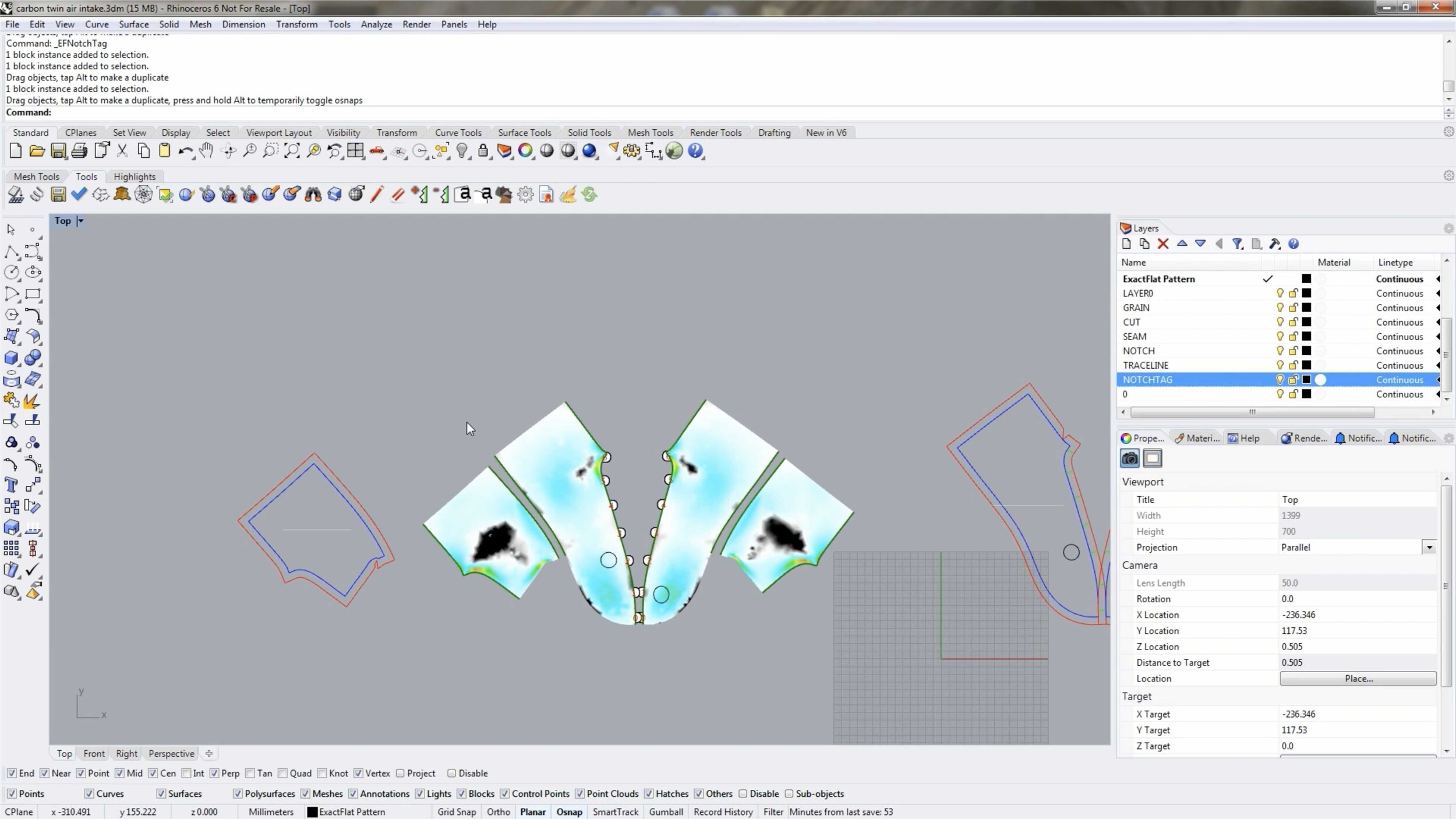